Sea Metal Industries - Brass Component Manufacturing
- Sea Metal Industries
- Posted by []
At Sea Metal Industries, our manufacturing process begins with the careful selection of high-grade raw materials, primarily copper and zinc, which are then melted to create a precise brass alloy. The molten metal is cast into billets or ingots, which are then heated and passed through rollers to form the required shapes.
We further refine the brass through cold rolling and drawing to ensure a smooth finish and improve its strength. Annealing is performed to relieve internal stresses and enhance workability. Finally, our skilled craftsmen use advanced machinery to machine, fabricate, and finish the components to meet precise specifications. Our rigorous quality control process ensures that each component is durable, corrosion-resistant, and meets the highest standards of performance.
The first step in our manufacturing process is melting the raw materials in a furnace at a controlled temperature. This creates a molten alloy, which is then poured into molds to form billets or ingots. These billets are allowed to cool and solidify, setting the foundation for further processing.
Once the billets have cooled, they are heated to a workable temperature and either passed through rollers or extruded into the desired shapes, such as rods, sheets, or wires. This step, known as hot rolling or extrusion, helps to form the brass into a manageable form for the next stages of processing.
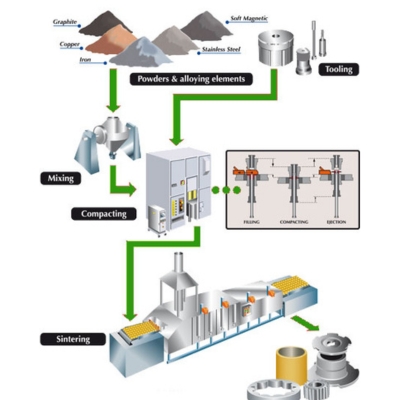
- Premium Brass Components: High-quality parts for various industries.
- Specialization: Fitting, electric, and gas parts manufacturing.
- Precision Engineering: Crafted with advanced technology.
- Corrosion Resistance: Ensuring durability and longevity.
- Custom Solutions: Tailored to meet specific client needs.
- Global Distribution: Serving clients worldwide.
- Timely Delivery: Committed to fast and reliable shipping.
- Customer Satisfaction: Focused on delivering excellence in every project.
Once the brass has been shaped through hot rolling or extrusion, it undergoes a process called cold rolling and drawing. During this stage, the brass is processed at room temperature to refine its shape and improve its strength. Cold rolling ensures that the brass has tighter tolerances and a smoother surface finish, which is essential for precision components. This step also enhances the material's mechanical properties, making it suitable for various industrial applications.
After cold rolling, the brass is subjected to annealing, a crucial process where it is heated to high temperatures and then slowly cooled. Annealing helps relieve any internal stresses in the material, making it easier to machine and form into precise shapes. This process also improves the overall workability of the brass, allowing us to achieve complex designs with ease. The annealed brass is now ready for machining.
In the machining and fabrication stage, our skilled technicians use advanced tools such as CNC machines, lathes, and drills to shape the brass into specific components. This process ensures that the brass parts meet the exact requirements of our clients. Whether it’s custom threads, precise dimensions, or complex designs, we can deliver components that fit perfectly into any application. Each part is carefully crafted to ensure it meets stringent specifications for quality and durability.
Finally, we focus on the surface treatment of the brass components. Polishing gives the parts a smooth, shiny finish, while plating with materials like nickel or chrome enhances corrosion resistance and improves the visual appeal. Protective coatings may also be applied to preserve the finish and ensure the longevity of the parts. The final step in the process is rigorous quality control. Every component undergoes comprehensive tests to ensure it meets the highest standards for dimensional accuracy, strength, corrosion resistance, and surface finish.
At Sea Metal Industries, we are committed to delivering the highest quality brass components for industrial and commercial applications. Our comprehensive manufacturing process guarantees that every product we produce is built to last, offering reliable performance for even the most demanding uses. From raw material selection to final inspection, our process ensures that we meet the needs of our clients with precision and excellence at every step.